Modular Barn
Delivery
Denco's Modular Barn Delivery & Setup
With our modular construction approach, we craft each barn in our shop and deliver it to your location. This helps us ensure the quality of the construction by working indoors, and reduces the time and intrusion required on your property. Here are the basic steps involved in the delivery and setup of a modular barn.
1. Site Prep
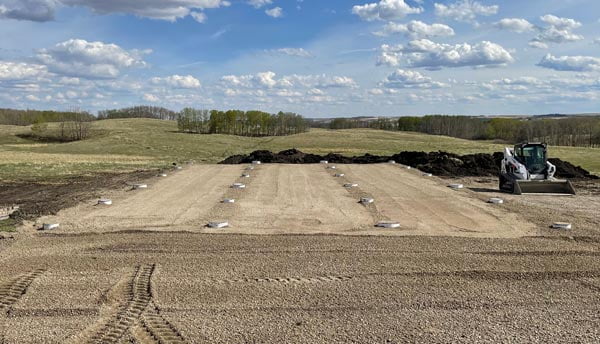
The site prep for a typical barn begins with stripping the topsoil. After the initial excavation, we install concrete piers for the barn foundation. (Note that the premier requires a full foundation and the stable suite only requires a gravel base.) We drill holes and pour piles, with 4 rows of 12-inch piers supporting each barn. This is typically done at least 2 weeks prior to actual setup, and when the concrete is dry we backfill with gravel.
2. Delivery
When actual barn setup begins, your barn will be delivered in sections—typically three sections for the western-style barns with a loft, and each side. A crane is used to set each section, and the main components can be placed quickly and efficiently.
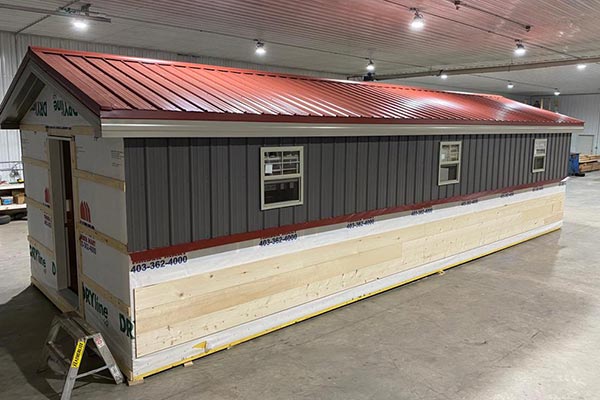
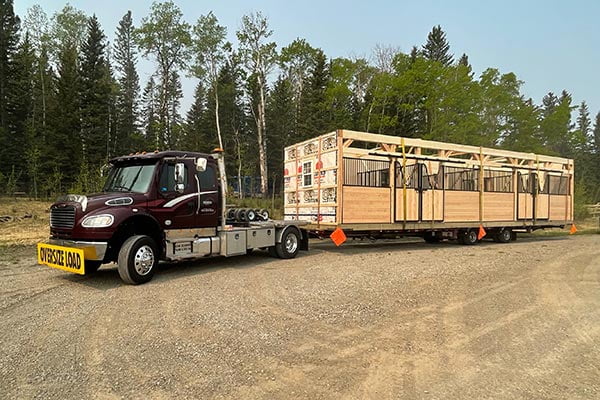
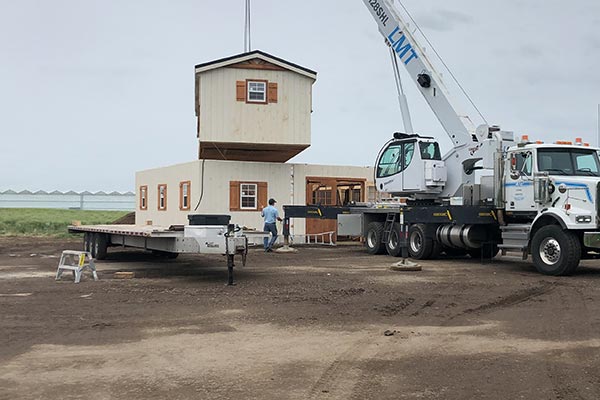
3. Barn Finalization
Once the main components are placed, the side roofs are framed and the barn ends are completed, and any finishing touches or options are finalized. Typically, from the time modules arrive to when the last screw is in is approximately 10 days.
FAQ
Do you provide financing?
We do our best to work with any financial institutions’ requirements, but do not offer in-house options at this time.
A typical project payment schedule is as follows: we require a deposit of $10,000 to book a build slot. On receipt, a projected date of the barns’ arrival is given. The second installment is due when the foundation piles are completed. The barn will then be delivered and set up onsite, which coincides with a third payment. The remaining balance is due when the project is fully completed.
What are my foundation options?
We recommend the installation of concrete piles for most of our barns. These are the most cost effective foundation and provide the best footing for your barn. We install these ourselves, ensuring your project is completed professionally and on time for the barn to be delivered. An alternative option is a concrete floating slab. This option costs more up front but offers a one-stop floor and can work well.
How much space is required for barn installation?
Space requirements vary with the style of barn. For installation of a western barn we need to be able to get the modules in from one end of the build site. Ideally there is enough space to maneuver a tele-handler around the barn once it is placed. A picker truck needs to be able to get within 20′ of the barn as it used to set the loft section on applicable buildings.